I. Introduction to Tank Cleaning
Definition and Importance of Tank Cleaning
Tank cleaning is a crucial process in various industries involving the storage and transportation of liquids, such as oil, chemicals, and other hazardous materials. It involves the removal of residues, contaminants, and sediments that accumulate inside tanks over time. Proper tank cleaning is essential to ensure the integrity of the storage facility, prevent contamination of stored materials, and maintain environmental safety standards.
Overview of Tank Cleaning Process
The tank cleaning process typically involves several steps, starting with preparation and inspection, followed by the actual cleaning procedure, and concluding with post-cleaning verification and waste disposal. Depending on the type of tank and the nature of its contents, different cleaning methods and equipment may be employed to achieve optimal results.
II. Understanding Oil Spills
Definition and Causes of Oil Spills
An oil spill refers to the accidental release of petroleum products into the environment, such as crude oil or refined fuels like gasoline or diesel. Oil spills can occur due to various factors, including equipment failure, human error, natural disasters, and acts of sabotage. These incidents pose significant environmental risks and can have devastating effects on ecosystems, wildlife, and human health.
Environmental Impact of Oil Spills
Oil spills can have far-reaching consequences on marine and terrestrial environments. They can contaminate water bodies, soil, and air, leading to habitat destruction, loss of biodiversity, and economic hardships for communities dependent on affected ecosystems. The long-term effects of oil spills can persist for years, requiring extensive cleanup and remediation efforts.
Importance of Proper Tank Maintenance to Prevent Oil Spills
Proper maintenance of storage tanks is critical to preventing oil spills and minimizing their environmental impact. Regular inspections, routine maintenance procedures, and adherence to safety protocols can help identify potential risks and address them before they escalate into catastrophic incidents. Implementing best practices for tank cleaning and maintenance is essential for ensuring operational safety and environmental stewardship.
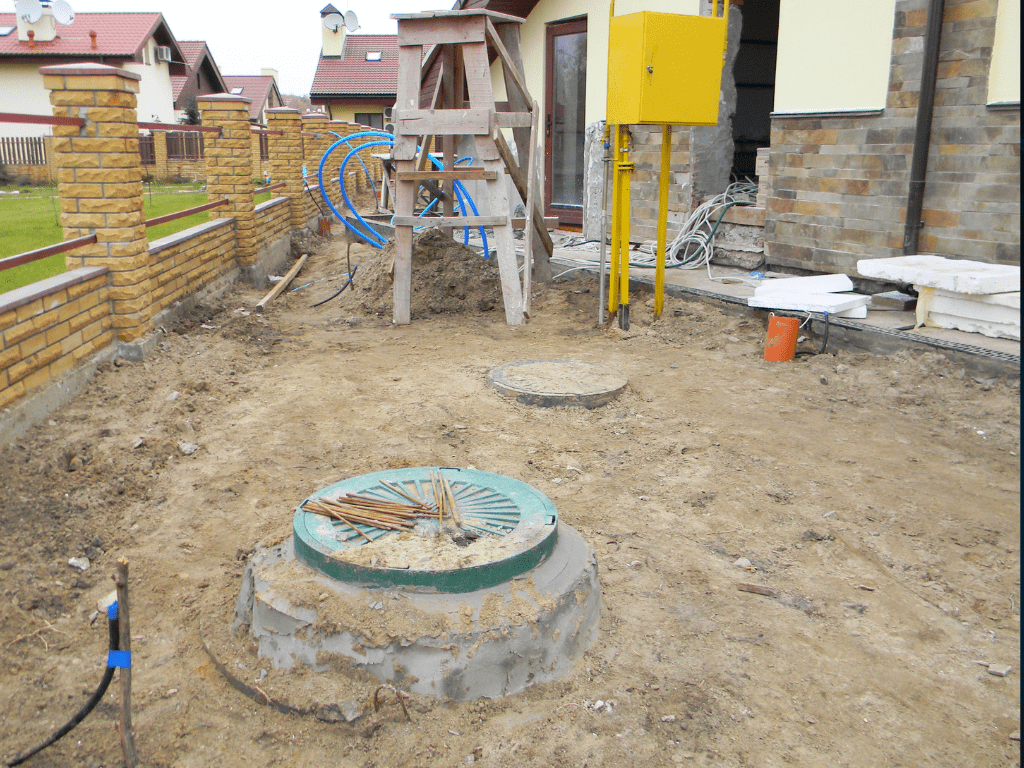
III. Tank Cleaning Techniques
Mechanical Cleaning Methods
1. Scrubbing and Scraping
Scrubbing and scraping are traditional mechanical cleaning methods used to remove solid residues and deposits from tank surfaces. This process involves manually or mechanically scrubbing the interior walls of the tank using brushes, scrapers, or abrasive materials to dislodge contaminants. While effective for removing heavy accumulations, this method may be labor-intensive and time-consuming.
2. High-Pressure Washing
High-pressure washing utilizes water jets at high pressure to dislodge and remove residues from tank surfaces. This method is particularly effective for cleaning large tanks with complex geometries or hard-to-reach areas. High-pressure washing can be combined with detergents or cleaning agents to enhance its effectiveness and reduce cleaning time.
Chemical Cleaning Methods
1. Use of Oil Spill Dispersants
Oil spill dispersants are chemical agents designed to break down and disperse oil slicks on water surfaces, facilitating their natural degradation by microorganisms. These dispersants work by reducing the surface tension of oil droplets, allowing them to mix more readily with water. While controversial due to potential environmental impacts, dispersants can be effective in mitigating the spread of oil spills and minimizing shoreline contamination.
2. Oil Spill Solutions and Break-down Agents
– Why use AQUAQUICK 2000?
AQUAQUICK 2000 is a highly effective cleaning agent specifically formulated for removing oils, fats, fuels, minerals, and other contaminants from various surfaces, including tanks. Its unique composition and properties make it a preferred choice for industries requiring efficient and environmentally safe cleaning solutions.
– AQUAQUICK 2000: Introduction and Features
AQUAQUICK 2000 has been a trusted cleaning product for many decades, with numerous accreditations, testimonials, and lab results attesting to its effectiveness and reliability. Its versatile formulation makes it suitable for a wide range of applications, from industrial tank cleaning to engine parts degreasing.
– Benefits of Using AQUAQUICK 2000
Using AQUAQUICK 2000 offers several benefits, including reduced cleaning time, cost savings, and improved safety for users and the environment. Its powerful cleaning action and ability to break down various contaminants make it an indispensable tool for maintaining clean and efficient tank systems.
– Testimonials and Accreditations
AQUAQUICK 2000 has garnered praise from companies and cleaning experts worldwide for its outstanding performance and reliability. Numerous testimonials and accreditations attest to its effectiveness in tackling tough cleaning challenges and delivering superior results compared to competing products.
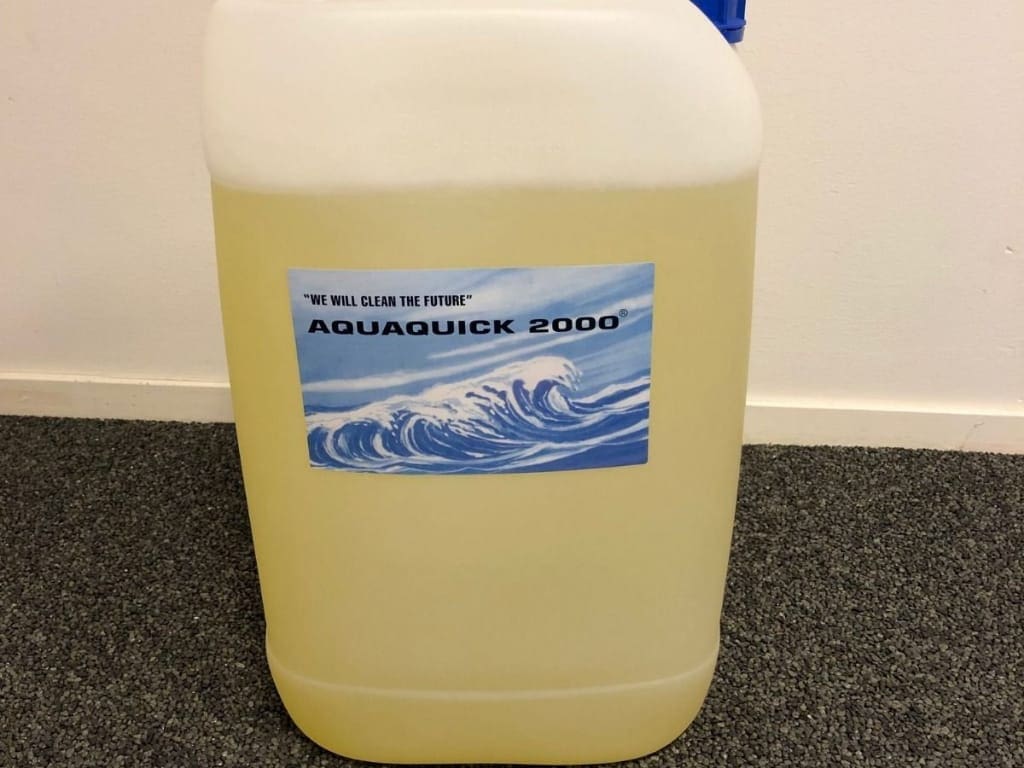
IV. Steps for Effective Tank Cleaning
A. Pre-Cleaning Preparation
1. Safety Precautions
Before initiating the tank cleaning process, it is essential to prioritize safety to prevent accidents and ensure the well-being of personnel involved. This includes:
- Conducting a thorough risk assessment to identify potential hazards such as toxic fumes, confined spaces, and electrical hazards.
- Providing appropriate personal protective equipment (PPE) such as respirators, gloves, and eye protection.
- Implementing lockout/tagout procedures to isolate energy sources and prevent accidental startup of equipment.
- Training personnel on emergency procedures, including evacuation routes and first aid protocols.
2. Drainage and Ventilation
Proper drainage and ventilation are critical aspects of tank cleaning to ensure the removal of liquids, gases, and vapors from the tank environment. This involves:
- Ensuring that the tank is completely emptied of its contents and that residual liquids are safely drained and disposed of according to regulatory guidelines.
- Implementing adequate ventilation systems, such as exhaust fans or forced-air blowers, to maintain a safe atmosphere within the tank and prevent the buildup of hazardous gases or vapors.
B. Cleaning Process
1. Inspection and Assessment
Before commencing the cleaning operation, a comprehensive inspection and assessment of the tank’s condition should be conducted. This includes:
- Visual inspection of the interior and exterior surfaces of the tank for signs of corrosion, structural damage, or contamination.
- Testing of tank contents to determine the presence of hazardous substances or residues.
- Evaluation of accessibility and potential obstacles that may impede the cleaning process.
2. Selection of Cleaning Method
Based on the findings of the inspection, the most suitable cleaning method should be selected to achieve effective removal of contaminants. This may include:
- Mechanical cleaning methods such as scrubbing, scraping, or high-pressure washing for removing solid residues and deposits.
- Chemical cleaning methods using specialized cleaning agents or detergents to dissolve and emulsify stubborn contaminants.
- Utilization of innovative technologies such as robotic cleaners or automated systems for large-scale or complex tank configurations.
3. Application of Cleaning Agents (AQUAQUICK 2000)
Incorporating effective cleaning agents like AQUAQUICK 2000 can significantly enhance the cleaning process by:
- Breaking down oils, fats, fuels, and other contaminants, making them easier to remove from tank surfaces.
- Facilitating the emulsification and dispersion of contaminants, preventing their re-adhesion to tank walls.
- Minimizing cleaning time and labor costs while maximizing cleaning efficiency and effectiveness.
C. Post-Cleaning Procedures
1. Inspection and Quality Control
Following the completion of the cleaning process, a thorough inspection and quality control assessment should be conducted to ensure that the tank is clean, safe, and ready for use. This includes:
- Visual inspection of tank surfaces for any remaining residues or contaminants.
- Testing of tank contents to verify cleanliness and compliance with regulatory standards.
- Conducting leak tests and integrity checks to confirm the structural integrity of the tank.
2. Waste Disposal
Proper disposal of waste generated during the tank cleaning process is essential to prevent environmental pollution and comply with regulatory requirements. This involves:
- Segregation of hazardous and non-hazardous waste according to regulatory classifications.
- Transporting and disposing of waste materials at authorized facilities or through licensed waste management providers.
- Maintaining accurate records of waste disposal activities, including manifests and certificates of disposal, for regulatory compliance and auditing purposes.
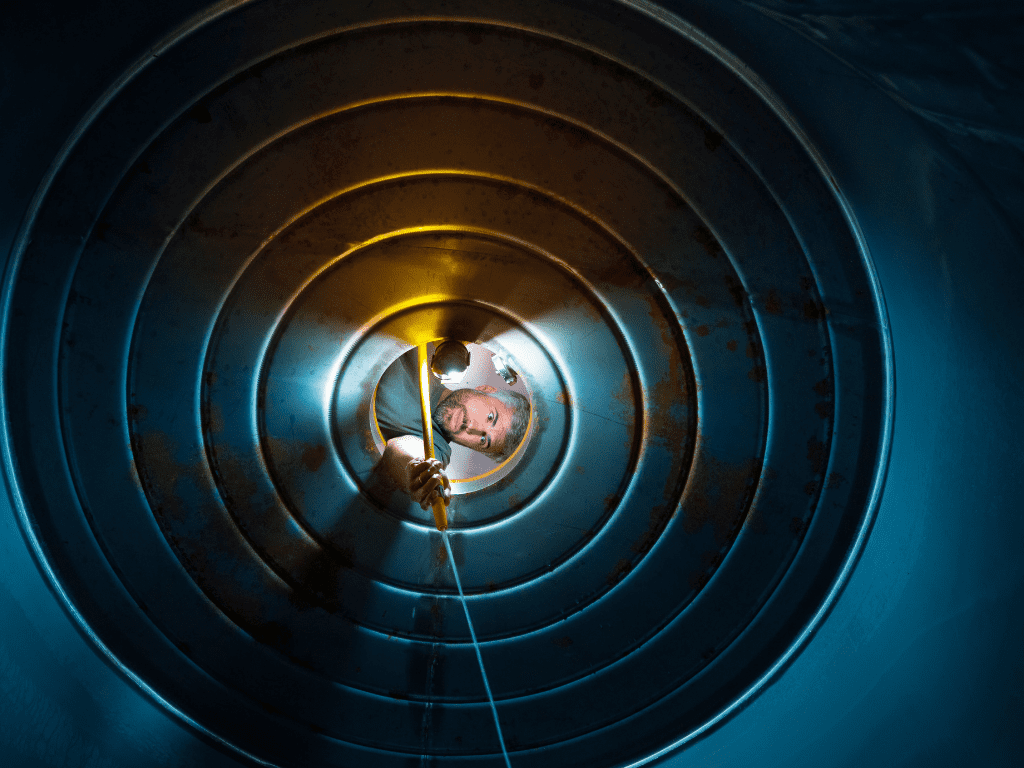
V. Tank Maintenance Practices
A. Regular Inspection and Monitoring
Regular inspection and monitoring of tanks are essential for identifying potential issues early and implementing corrective measures to prevent costly downtime or accidents. This includes:
- Scheduled visual inspections of tank surfaces, fittings, and accessories for signs of corrosion, leaks, or structural damage.
- Monitoring of tank levels and pressures to detect abnormalities or deviations from normal operating parameters.
- Implementing predictive maintenance techniques such as ultrasonic testing or thermal imaging to identify potential failure points before they occur.
B. Grease Trap Maintenance
1. Understanding Grease Traps
Grease traps, also known as grease interceptors or grease separators, are plumbing devices designed to intercept and trap fats, oils, and grease (FOG) from wastewater streams to prevent them from entering the sewer system and causing blockages or pollution.
2. Proper Grease Trap Sizing
Ensuring that grease traps are properly sized and installed according to regulatory requirements and industry standards is essential for their effective operation. Factors to consider include:
- The flow rate and volume of wastewater generated by the facility.
- The concentration of fats, oils, and grease (FOG) in the wastewater stream.
- The design and configuration of the grease trap, including baffle placement and outlet structure.
3. Maintenance Schedule
Establishing a regular maintenance schedule for grease traps is crucial to prevent buildup and blockages that can lead to costly repairs or regulatory violations. This includes:
- Routine inspection and cleaning of grease traps to remove accumulated FOG and solid residues.
- Replacement of worn or damaged components such as baffles, seals, or lids to maintain proper functionality.
- Documentation of maintenance activities and adherence to regulatory reporting requirements.
C. Prevention of Corrosion and Contamination
Implementing proactive measures to prevent corrosion and contamination of tanks is essential for prolonging their service life and ensuring the integrity of stored materials. This includes:
- Applying protective coatings or linings to tank surfaces to resist corrosion and chemical degradation.
- Implementing corrosion control measures such as cathodic protection or corrosion inhibitors to mitigate corrosion risks.
- Implementing spill containment and secondary containment measures to prevent leaks and environmental contamination in the event of a tank failure.
VI. Tank Cleaning Equipment and Tools
A. Overview of Essential Equipment
Tank cleaning requires various equipment and tools to ensure efficient and thorough cleaning processes. Some essential equipment includes:
- High-Pressure Washers: These machines use pressurized water to remove dirt, grime, and residues from tank surfaces. They are particularly effective for cleaning large tanks and removing stubborn contaminants.
- Scrubbing Brushes and Scrapers: Manual or mechanical brushes and scrapers are used to scrub and scrape away solid residues and deposits from tank walls, corners, and crevices.
- Vacuum Trucks: Vacuum trucks are used to suction out liquids, sludge, and debris from tanks, providing thorough cleaning and waste removal capabilities.
- Chemical Sprayers and Applicators: Equipment for applying cleaning agents, detergents, and disinfectants to tank surfaces, facilitating the breakdown and removal of contaminants.
- Personal Protective Equipment (PPE): Safety gear such as gloves, goggles, respirators, and protective clothing is essential to protect workers from exposure to hazardous chemicals, fumes, and physical hazards during tank cleaning operations.
B. Selection Criteria for Cleaning Equipment
When selecting tank cleaning equipment, several factors should be considered to ensure optimal performance and safety:
- Tank Size and Configuration: Choose equipment that is suitable for the size and geometry of the tank being cleaned, ensuring that all areas are accessible and effectively cleaned.
- Type of Contaminants: Select cleaning equipment and agents based on the type and composition of contaminants present in the tank, ensuring compatibility and effectiveness in removing specific residues.
- Safety Features: Prioritize equipment with built-in safety features such as automatic shutoff valves, pressure relief mechanisms, and ergonomic design to minimize the risk of accidents and injuries.
- Environmental Considerations: Choose equipment and cleaning agents that are environmentally friendly and compliant with regulatory standards to minimize pollution and protect ecosystems.
- Cost and Efficiency: Consider the cost-effectiveness and efficiency of the equipment, taking into account factors such as cleaning speed, labor requirements, and maintenance costs over the equipment’s lifespan.
C. Emerging Technologies in Tank Cleaning
Advancements in technology continue to drive innovation in tank cleaning, leading to the development of new tools and techniques for improved efficiency and effectiveness. Some emerging technologies in tank cleaning include:
- Robotic Cleaners: Autonomous robotic systems equipped with sensors and cameras for navigating and cleaning tanks, offering precise and thorough cleaning capabilities while reducing the need for human intervention in hazardous environments.
- Ultrasonic Cleaning Systems: Ultrasonic cleaning technology uses high-frequency sound waves to agitate cleaning solutions, effectively removing contaminants from tank surfaces without the need for harsh chemicals or abrasive scrubbing.
- Green Cleaning Agents: Environmentally friendly cleaning agents made from biodegradable and renewable materials, offering effective cleaning performance while minimizing environmental impact and reducing health risks for workers.
- Remote Monitoring and Control Systems: Advanced monitoring and control systems allow for real-time monitoring of tank conditions, remotely adjusting cleaning parameters and optimizing cleaning processes for efficiency and safety.
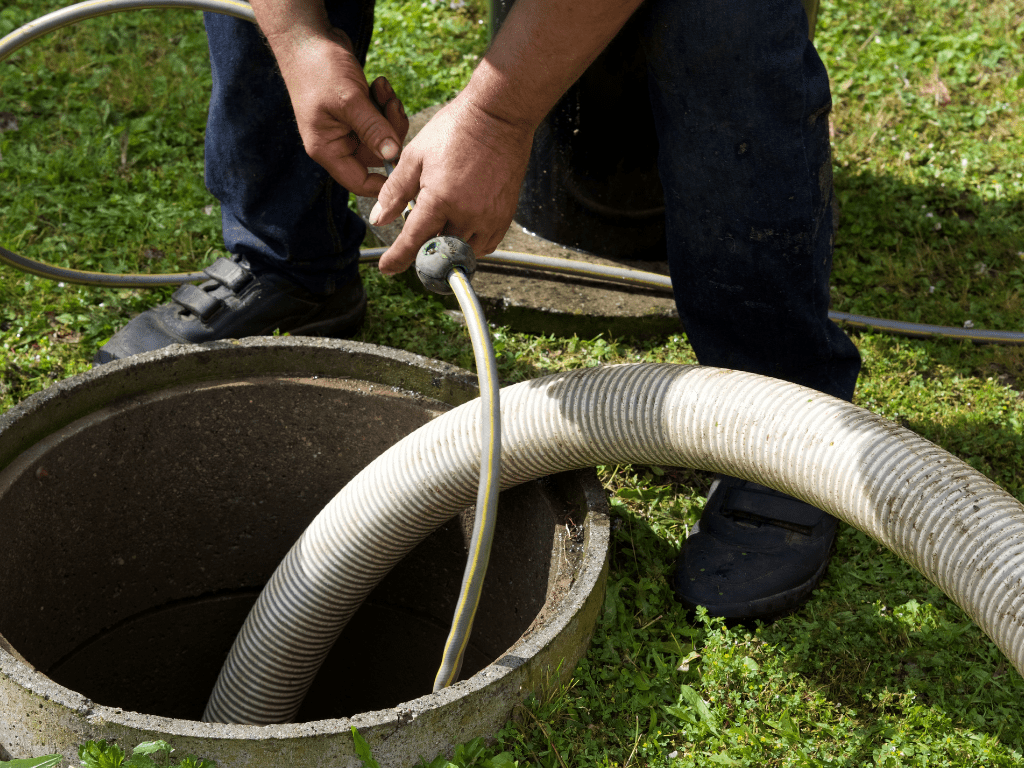
VII. Best Practices for Effective Tank Maintenance
Sharing best practices for effective tank maintenance can help promote industry standards and guidelines for ensuring the long-term integrity and performance of storage tanks. Best practices may include:
- Establishing routine inspection and maintenance schedules to identify and address potential issues before they escalate into costly repairs or environmental hazards.
- Implementing proactive measures such as corrosion control, leak detection, and integrity testing to prevent tank failures and ensure compliance with regulatory requirements.
- Training personnel on proper cleaning procedures, safety protocols, and environmental stewardship practices to promote a culture of accountability and responsibility in tank maintenance operations.
Conclusion
A. Summary of Key Points
In summary, effective tank cleaning and maintenance are essential for ensuring operational safety, environmental protection, and regulatory compliance in various industries. Key points discussed include:
- The importance of thorough pre-cleaning preparation, selection of appropriate cleaning methods and equipment, and adherence to post-cleaning procedures for optimal results.
- The significance of regular tank maintenance practices, including inspection, monitoring, and preventive measures, in preventing accidents, spills, and contamination incidents.
- The role of emerging technologies in driving innovation and efficiency in tank cleaning processes, as well as the importance of continuous improvement and adaptation to industry trends and regulations.
B. Importance of Regular Tank Maintenance
Regular tank maintenance is crucial for preventing costly downtime, environmental damage, and safety hazards associated with tank failures and contamination incidents. By implementing proactive maintenance strategies and adhering to best practices, companies can ensure the long-term integrity and performance of their tank systems while minimizing risks and maximizing operational efficiency.
C. Future Trends in Tank Cleaning and Maintenance
Looking ahead, future trends in tank cleaning and maintenance are likely to focus on sustainability, automation, and digitization. Innovations such as green cleaning agents, robotic cleaners, and remote monitoring systems are expected to play a significant role in improving efficiency, reducing environmental impact, and enhancing safety in tank maintenance operations. As technology continues to evolve and regulatory requirements evolve, companies must remain adaptable and proactive in embracing new approaches and solutions to meet emerging challenges and opportunities in tank cleaning and maintenance.